Fab-Wide Scheduling of Semiconductor Plants: A Large-Scale Industrial Deployment Case Study
Decision-making in wafer fabs is a two-level problem. On one hand, fab-wide scheduling is tasked with the strategic management of factory assets. On the other hand, toolset-level scheduling focuses on the operation of individual work centres.
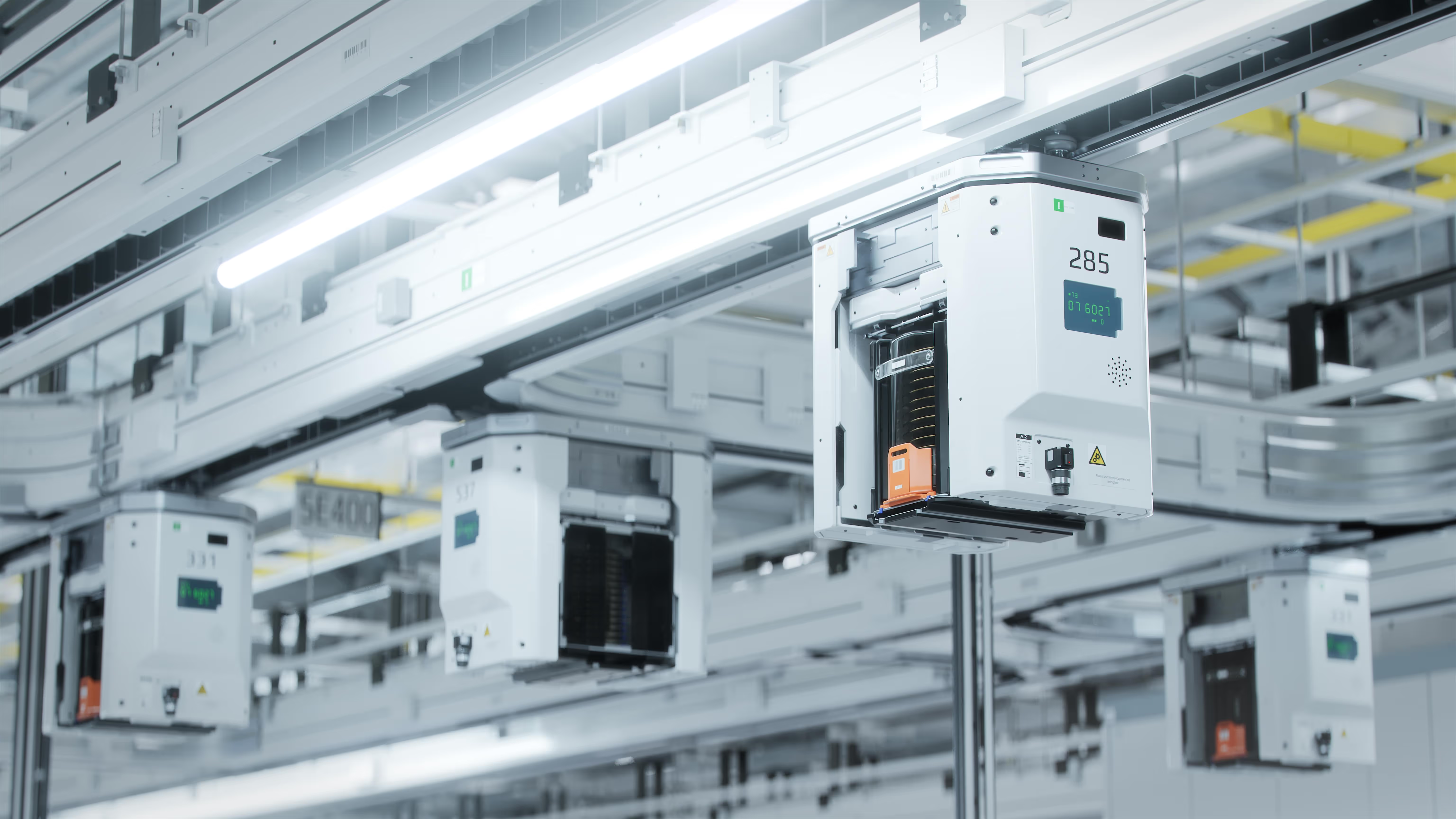
This article draws from the contents of a paper presented at Winter Simulation Conference 2022, titled: “Fab-Wide Scheduling of Semiconductor Plants: A Large-Scale Industrial Deployment Case Study”.
An Introduction to Fab-Wide Scheduling
The semiconductor industry is one of the largest and most complex industries in the world. The critical factors in semiconductor manufacturing are the ability to rapidly develop and test novel technologies, improve manufacturing processes to reduce rework and waste, as well as meet production targets in terms of prescribed volumes and due dates. In this context, high quality scheduling is of paramount importance.
Due to the long cycle times, where a wafer is processed over a span of months, decision-making in semiconductor fabrication plants (fabs) is typically framed as a two-level problem. On one hand, global scheduling (or fab-wide) is tasked with the strategic management of factory assets while considering all work-in-progress, incoming and outgoing flows across the fab, expected resource availability and other constraints. On the other hand, local (or toolset-level) scheduling focuses on the operation of individual work centres. It is typically tasked with identifying the best immediate dispatch decisions i.e. which jobs waiting for dispatch should be assigned to which available machine.
Most development efforts to date have focused on the shorter time frame dispatch decisions i.e. local scheduling. This is a more manageable problem since there is little look-ahead and the scope is limited to a single or a few toolsets. Despite numerous research efforts, to date there has not been a published case study of a fab-wide scheduler successfully deployed in a large semiconductor manufacturing facility. Nevertheless, the potential for improvement at the fab-wide level is tremendous; there are numerous opportunities to improve throughout and have a step change in performance. For example:
- Bottlenecks occur due to repetition of process loops, high-cost machines with low capacity, and other physical or operational constraints. To manage them, a strategic approach is needed that looks at the bigger picture and avoids early dispatch of wafers that will end up in a bottleneck area.
- WIP flow control mechanisms (kanbans) are important for quality control but can block high-priority wafers. Fab-wide scheduling can greatly improve this aspect of operation.
- Timelinks (also known as timeloop, time lag, or qtime constraints) are challenging because they define the minimum or maximum amount of time between two or more consecutive process steps, leading to a conundrum of keeping downstream machines idle or not. Fab-wide scheduling can greatly assist by accurately predicting arrival times and deciding when to trigger timelinked lots.
Methodology
The scheduling framework proposed in this blog is hierarchical and consists of two main components which run independently and at different frequencies — the Toolset Scheduler (TS) and Fab-Wide Scheduler (FWS).
The Toolset Scheduler considers the currently in-process and/or upcoming process step of all wafers in the cluster.
FWS takes a view of the entire fab at once and considers multiple future steps for each wafer. It focuses on improving schedule quality by considering the flow of wafers through the fab, something the toolset scheduler cannot do due to its singlestep, toolset-level nature. The main purpose is to redirect flow through the fab and thereby improve flow linearity, reduce bottlenecks, improve WIP flow control management, and reduce timelink violations. Our FWS approach achieves this by predicting wait/cycle times for multiple future steps, analysing those predicted wait/cycle times with respect to the different areas of potential improvement, and re-prioritising wafer steps in a way that guarantees improved (weighted) cycle times. In brief, FWS combines two main elements: (i) an operational module that captures in full detail all relevant constraints e.g. detailed process time modelling, machine maintenance, shift changes, dynamic batching constraints, kanbans etc. (ii) a search module that identifies beneficial priority changes given the evolving fab conditions and state features.
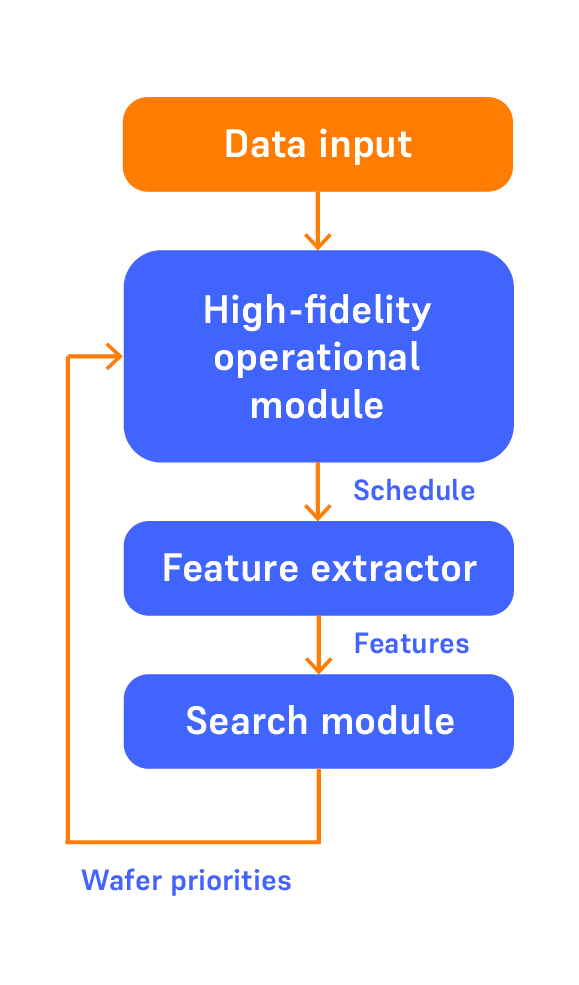
FWS communicates with the toolset schedulers via priority weights (and some other predicted timing information) for individual steps of a wafer, as shown in Figure 2. An advantage of our approach is that, while FWS always schedules all tools in the fab, users can specify which toolsets are subject to guidance; FWS adjusts its search accordingly. This is particularly useful for gradually rolling out FWS in a fab and evaluating its impact. In addition, the guidance strength is controllable - although full guidance is the optimal choice, tuning down guidance allows for a more gradual deployment.
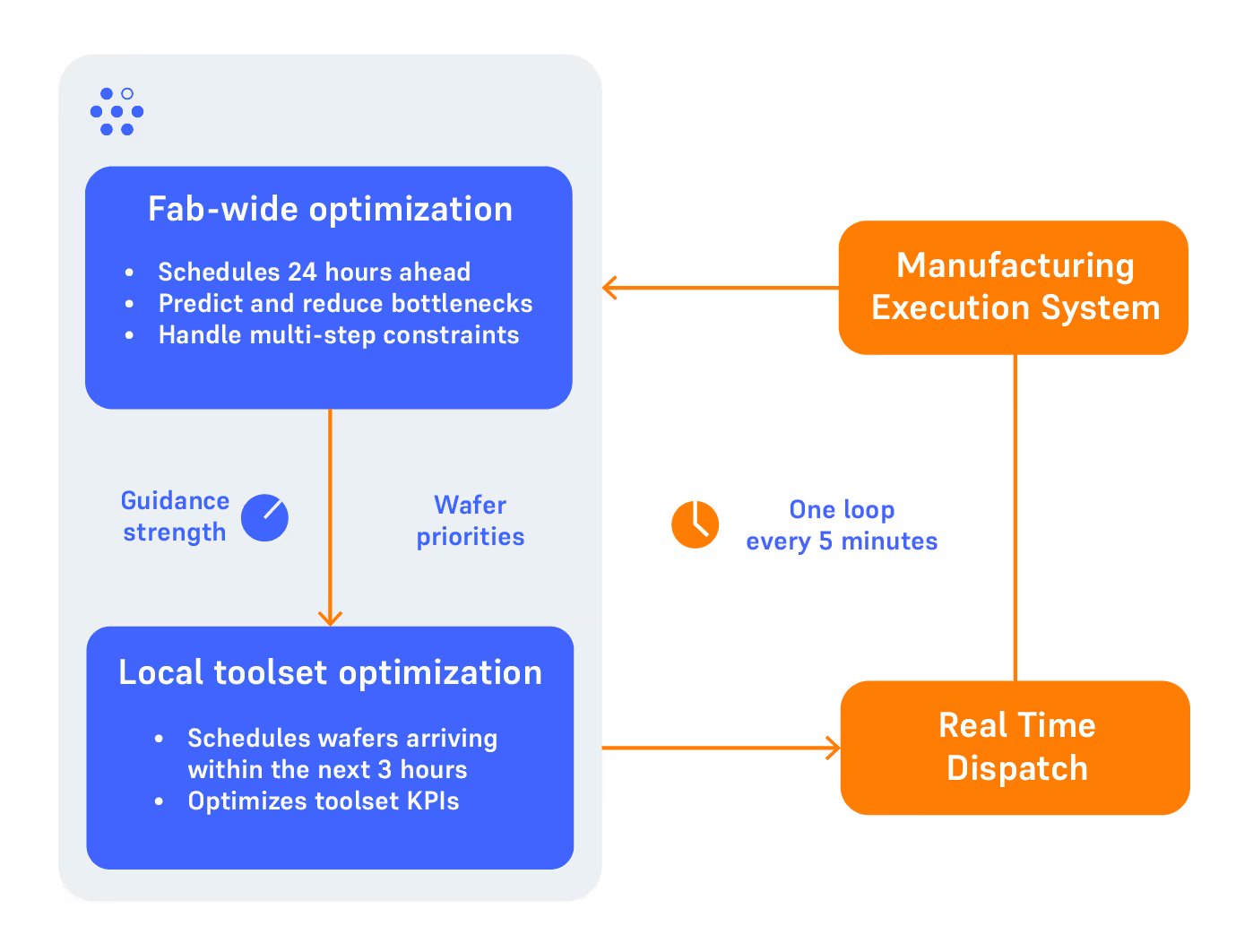
Seagate Deployment
Seagate is a world leader in data storage technology, with more than 40% share of the global Hard Disk Drive (HDD) market. The Springtown facility in Northern Ireland produces around 25% of the total global demand for recording heads, the critical component in a HDD. Flexciton’s FWS / TS scheduling system was trialled in Seagate Springtown between March-May 2022. After successful testing, the system has been operational 24/7 since June 2022; a timeline is shown in Figure 3.
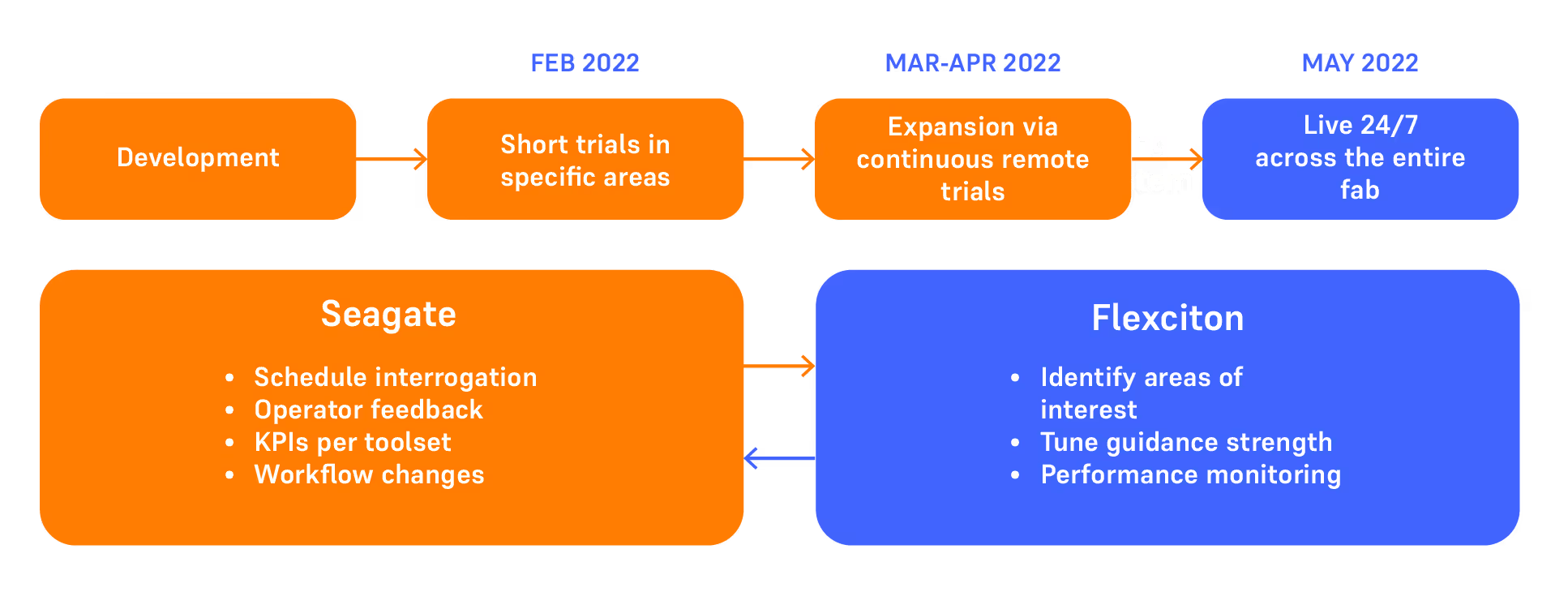
It is important to note that deploying and testing a novel piece of technology in a large factory that runs around the clock presents many practical challenges to be overcome:
- Controllability (scope): important to ensure that the new development is deployed in a controlled manner. The FWS-TS guidance scheme allows for localised trials, where focus can be placed on problematic areas and gradually increase scope.
- Controllability (magnitude): it is useful to only focus on cases with obvious merit first. This is achieved by controlling guidance strength.
- Explainability: important to be able to detect and reason about the changes. This is achieved by a combination of UI features and support tools which have been designed to give operators and managers situational awareness.
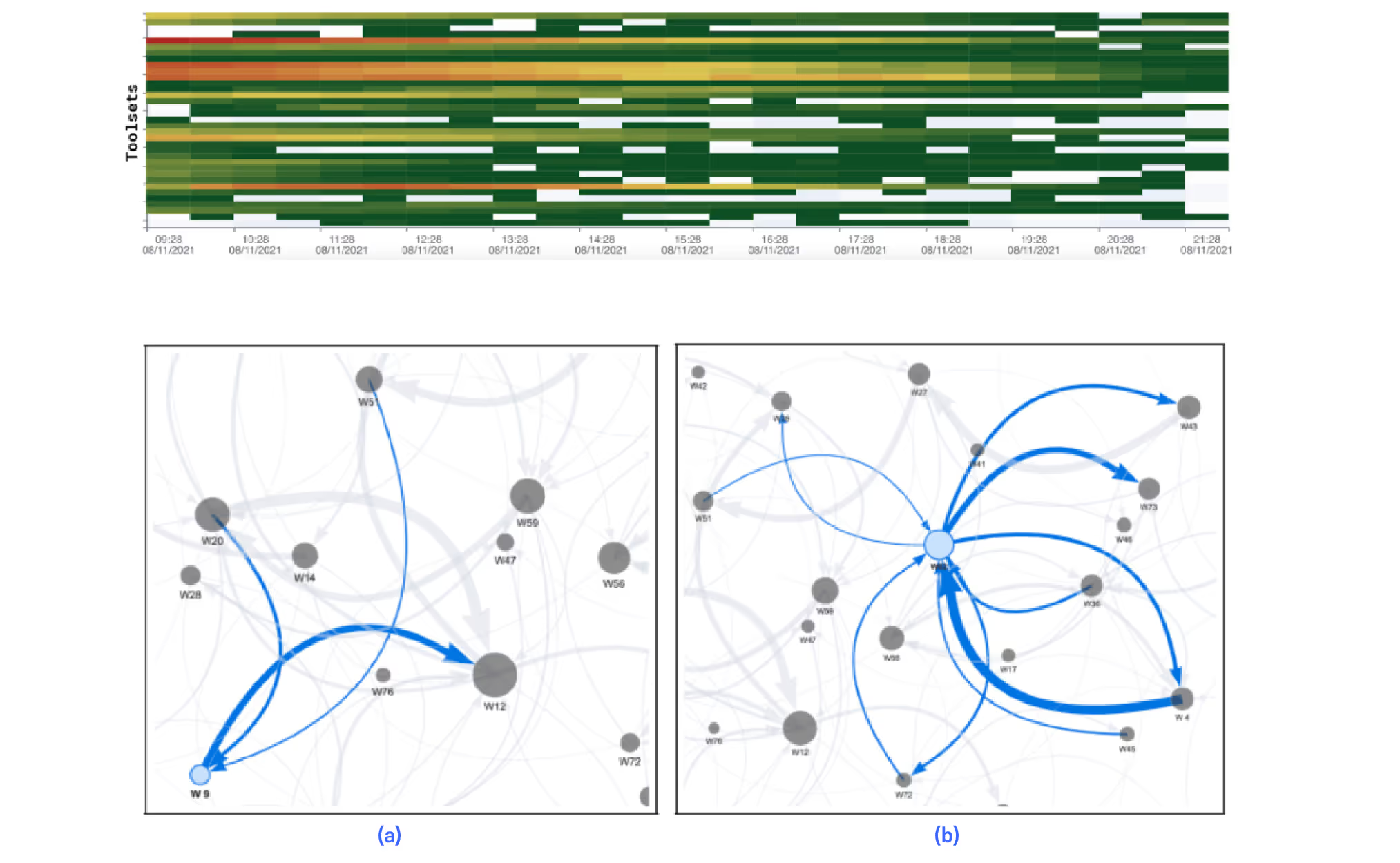
Results and Learnings
Quantifying the benefit of an alternative scheduling approach remains a challenging task. When deployed in a real plant, traditional A/B testing between pre and post-deployment suffer from (i) dynamic fab conditions (ii) an ever-changing product mix and (iii) evolving capabilities of the fab e.g. increased/decreased labour capacity and new tool commissioning/decommissioning.
As such, it was decided to look at the impact from different angles - a statistically significant impact would be expected to result in a substantial shift in numerous business processes and metrics. In particular, three different aspects were examined.
- Deep dives on specific toolsets and metrics.
- Comparison against internal simulation and planning tools.
- Observing the impact on manual interventions.
Notably, all three approaches indicated a change in fab performance between pre and post-deployment; more details will be shared in future articles. In the Winter Sim Conference paper presented in December 2022, we focused on the latter point; A proxy we can use for this benefit is the volume of ad hoc control flow rules activated/deactivated in the fab. Every day, specialists have to define numerous, in some cases even hundreds, of ad hoc control flow rules to better manage operations given the prevalent conditions. For example, setting a ”hard down” rule, where lots are manually placed on hold so as not to continue to a downstream bottleneck. In Figure 5, we show the number of ad hoc operational rules implemented in the Seagate Springtown fab between weeks 2 and 26 of the year 2022 (i.e. from early January until late June). As can be seen in the final weeks, the number of ad hoc rule transactions averaged less than 150 per week, a decrease of over 300% compared to the pre-deployment period. This is strong evidence that FWS deployment reduced massively manual interventions required to effectively control flows within the fab.
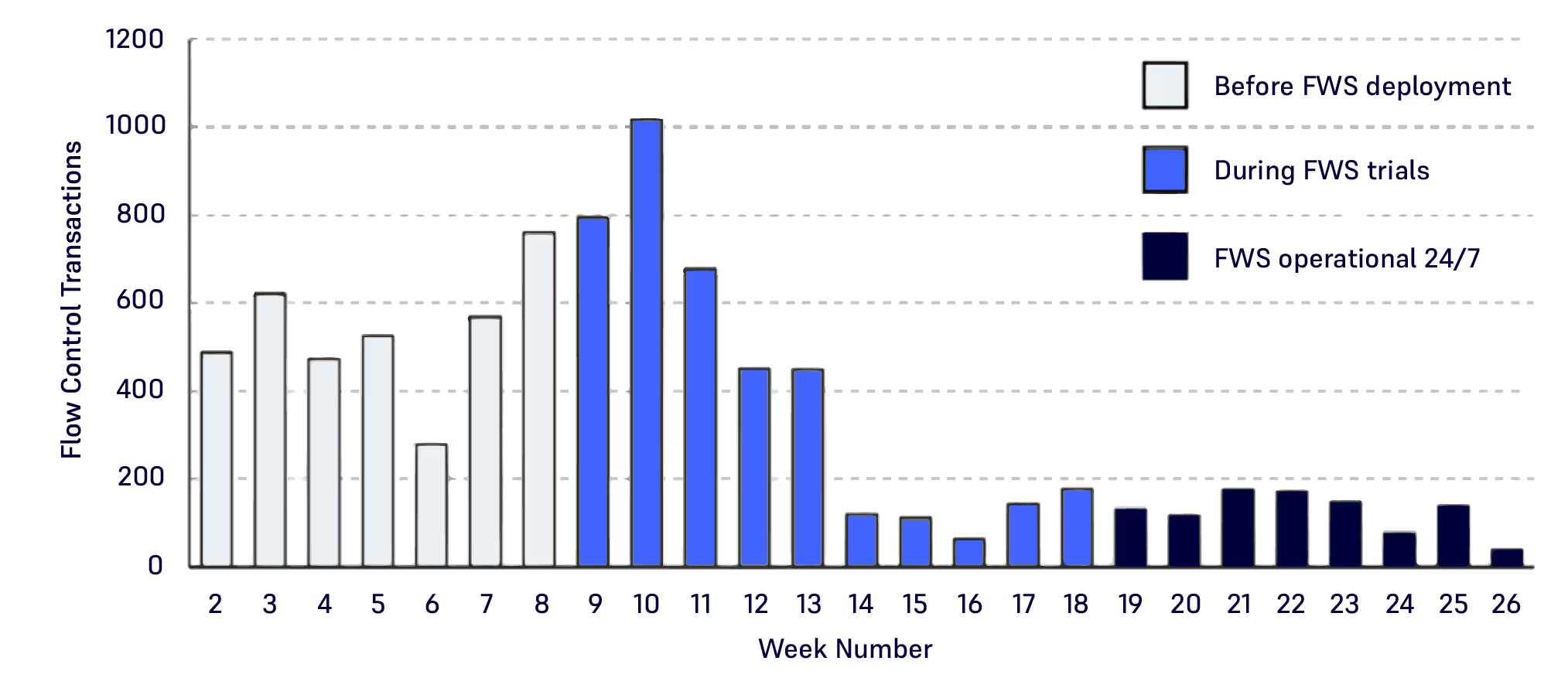
Conclusions
The main takeaway of the Winter Sim paper is that the increased horizon look-ahead and global nature of FWS presents numerous opportunities for a step change in factory KPIs. The Flexciton FWS was successfully trialled at Seagate Springtown over 3 months in 2022 and has been fully enabled across the fab since June 2022. It resulted in a radical decrease of interventions previously used to manually control wafer flows. Further analysis suggests that Flexciton’s TS and FWS schedulers have achieved substantial improvements in throughput and cycle times.
Author: Ioannis Konstantelos, Principal Engineer
More resources
Stay up to date with our latest publications.